%20(1).png)
Revolutionising Oil & Gas Exploration
Harnessing AI and Connectivity Management
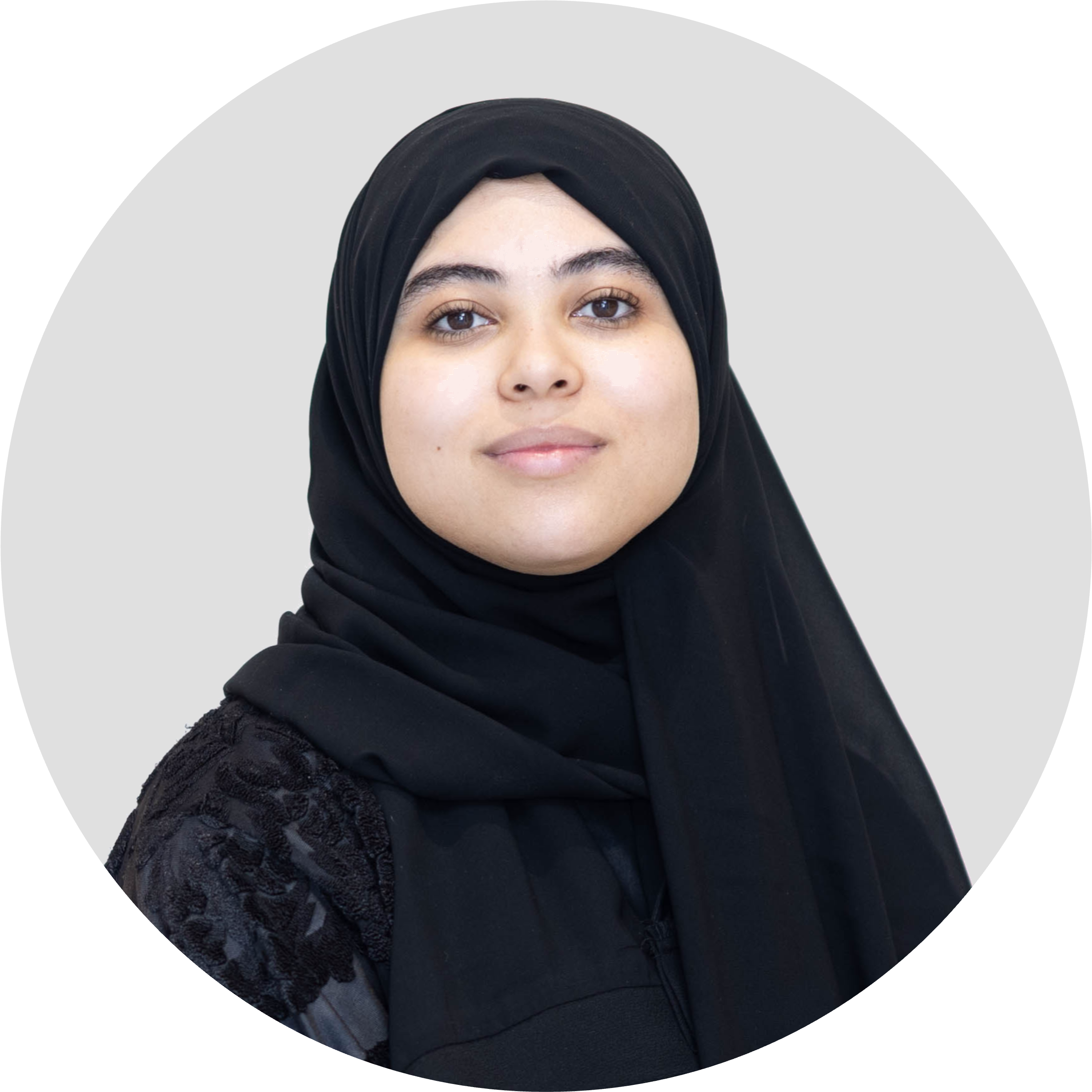
With the integration of artificial intelligence and connection management, the oil and gas industry is experiencing a transition. The desire to optimise exploratory operations and enhance operational efficiency is driving this change.
Machine learning and deep learning have the capacity to analyse vast amounts of data and derive significant insights for decision-making.
These methods may be used in a variety of facets of exploration, including seismic data processing, reservoir characterisation, and well design.
Connectivity management is critical to the oil and gas industry's seamless integration of artificial intelligence technology. It entails the efficient and dependable flow of data between various exploration process components such as sensors, data storage systems, and computational resources.
Leveraging Artificial Intelligence for Improved Seismic Interpretation and Reservoir Prediction
By recognising and analysing geological patterns using machine learning approaches, Artificial intelligence systems can lead to more accurate reservoir projections and better decision-making. These algorithms can examine vast volumes of data, such as seismic data, well logs, and production history, to uncover patterns and linkages that people may miss. Artificial intelligence algorithms can anticipate reservoir behaviour and attributes such as lithofacies, porosity, permeability, and subsidence risk by training on historical data and learning from prior reservoir characteristics. These forecasts can assist geoscientists and engineers in better understanding complicated subsurface geological trends and making educated decisions regarding reservoir management, exploration, and production methods.
Furthermore, artificial intelligence algorithms may help with the integration of various data sources, including seismic data, well logs, and production data, in order to give a full knowledge of reservoir features and optimise workflows for infill drilling operations. Artificial intelligence algorithms may save time and money, reduce uncertainty, and improve the accuracy of reservoir predictions and decision-making processes in the oil and gas business by automating data processing and interpretation.
Deep learning models, in particular, have transformed seismic interpretation by automating complicated operations, decreasing human error, and considerably speeding up the process. By training artificial intelligence models on past data, they may learn to recognise trends and forecast geological formations like faults and folds, as well as identify prospective reservoirs.
Additionally, AI-powered systems may be customised for specific conditions or geological formations to ensure maximum performance. These solutions may also be enhanced regularly through machine learning, improving their accuracy over time.
Artificial intelligence can improve reservoir prediction by assessing a wide range of data sources, including seismic characteristics, well logs, and geological models, to identify reservoir features like porosity, permeability, and hydrocarbon saturation.
The oil and gas industry can reap numerous benefits by employing artificial intelligence for enhanced seismic interpretation and reservoir prediction:
- Faster and more precise identification of probable reservoirs, lowering exploration risks and costs.
- Better decision-making across the exploration and production processes, resulting in better resource allocation and operational efficiency.
- Improved collaboration and communication across interdisciplinary teams, allowing for a more thorough understanding of underlying geology.
- Greater flexibility to shifting market conditions and industry demands as a result of continual Artificial Intelligence developments and improvements.
The use of artificial intelligence in seismic interpretation and reservoir prediction is altering the oil and gas business by allowing for better informed decision-making, lowering exploration risks, and saving considerable time and money. As artificial intelligence technology advances, operators can expect even higher levels of accuracy, efficiency, and productivity in their exploration efforts.
Optimising Drilling Operations through AI-Powered Automation
Artificial intelligence has emerged as a major changer in the oil and gas business, notably in improving drilling operations. Companies may use AI-powered automation to expedite different areas of the drilling process, such as real-time data analysis and drilling parameter optimisation, as well as automated control systems. This improves productivity, safety, and precision while also considerably lowering operational costs.
- Real-time data analysis: Drilling operations create large volumes of data covering a wide range of variables such as pressure, temperature, and torque. AI-powered systems can analyse and analyse this data in real time, providing the drilling team with information about subsurface conditions and possible concerns. This enables proactive drilling plan tweaks and enhancements, decreasing non-productive time and improving overall performance.
- Drilling parameter optimisation: Artificial intelligence algorithms can autonomously discover ideal drilling parameters such as bit weight, rotary speed, and flow rate while taking into consideration formation features and drilling circumstances. This reduces vibrations, wear and tear on the equipment, and overall drilling process optimisation, resulting in improved rates of penetration and cost savings.
- Automated control systems: AI-driven automation may be implemented into drilling control systems, allowing for greater precision and consistency in drilling job execution. Without the need for ongoing human interaction, these systems can automatically alter drilling settings and respond to changing conditions. Not only does this reduce human mistake and increase safety, but it also increases the efficiency and precision of drilling operations.
- Predictive maintenance: AI-powered systems may identify and prevent prospective equipment breakdowns or maintenance needs by combining historical data with real-time data from sensors and equipment. Companies may decrease downtime, increase equipment longevity, and save money by employing predictive maintenance practices.
- Enhanced safety and risk mitigation: During drilling operations, AI-powered analytics can monitor and detect possible dangers, allowing for proactive safety measures and better informed decision-making. As a consequence, risks are reduced, staff and equipment are better protected, and regulatory compliance is enhanced.
The deployment of AI-powered automation in the oil and gas sector greatly contributes to improving drilling operations. As artificial intelligence technologies evolve, firms may expect even higher precision, efficiency, and safety in their drilling operations, resulting in lower costs and increased profitability.
Revolutionary Connectivity Management Solutions in Oil and Gas Exploration
Effective connection management is critical in the oil and gas business, particularly in exploratory activities where precise and timely data transfer is critical. Remote sensing, Internet of Things (IoT) devices, and improved communication networks are revolutionising the way corporations do exploration, assuring uninterrupted data transfer and greater productivity.
- Remote sensing: Remote sensing technology enables data collecting without direct contact with the target region, making it an important tool for monitoring land, seas, and the atmosphere. Satellite-based remote sensing delivers high-resolution photos and data on surface geology, topography, and vegetation changes in oil and gas exploration, which may be used to detect probable hydrocarbon resources and decrease exploration risk. Furthermore, airborne remote sensing techniques such as Light Detection and Ranging (LiDAR) can offer detailed information on topography and features buried beneath vegetation, assisting in the evaluation of suitable exploration areas.
- IoT devices: The Internet of Things (IoT) is reshaping the oil and gas sector by linking physical items such as sensors, drilling equipment, and monitoring systems to internet-enabled platforms. IoT devices gather, transmit, and analyse real-time data, allowing for greater decision-making and efficiency. IoT devices can continually monitor drilling operations, equipment status, and ambient factors in exploration, enabling for more dependable and adaptable operations. Furthermore, IoT devices may aid in the monitoring and control of emissions, guaranteeing compliance with environmental requirements and lowering the environmental effect of the company.
- Advanced communication networks: When it comes to aiming for a unique way to express yourself, then here is the place to be. Satellite systems, fibre-optic connections, and wireless networks, for example, provide smooth data transfer, real-time collaboration, and better decision-making. These connectivity solutions address the obstacles of working in remote and complicated situations, allowing businesses to stay connected even in the most remote locations.
- Edge computing and data processing: The requirement for effective data processing and management has grown critical as the volume of data generated by exploratory operations has increased. Edge computing allows data to be processed and analysed closer to its source, decreasing network latency and the requirement for ongoing communication to faraway data centres. This enables speedier decision-making and optimisation of exploratory efforts, which leads to enhanced efficiency and cost savings.
Innovative connection management systems are transforming the oil and gas exploration environment by increasing efficiency and providing smooth data delivery. Companies may remain ahead of the curve by adopting and integrating cutting-edge technologies.
Implementing Digital Twins for Enhanced Oil and Gas Exploration
Digital twins are virtual replicas of physical assets, systems, or processes that mimic their real-world counterparts with exceptional precision. Leveraging real-time data, advanced digital technologies, and simulation capabilities, digital twins provide valuable insights, optimise performance, and facilitate informed decision-making. In the oil and gas industry, digital twins can be employed to create virtual models of oil and gas assets, enhancing the accuracy, efficiency, and cost-effectiveness of exploration processes.
The construction of digital twins involves integrating data from multiple sources, such as sensors, geological data, and operational records, to build a comprehensive representation of an asset. These virtual models are continuously updated with real-time data, ensuring they accurately reflect the current state of the physical asset. With the aid of sophisticated analytics and simulation software, digital twins can be used to forecast future performance, identify potential issues, and optimise operations.
Implementing digital twins for oil and gas exploration offers a range of benefits, including:
- Enhanced Decision-making: Digital twins enable real-time monitoring and analysis of subsurface conditions, drilling operations, and reservoir performance. This provides exploration teams with valuable insights to inform decision-making and prioritise resources effectively.
- Improved Accuracy and Efficiency: Digital twins can simulate various scenarios and conditions, helping exploration teams optimise drilling parameters, reduce non-productive time, and mitigate risks associated with exploration activities.
- Reduced Operational Costs: By using digital twins to forecast equipment maintenance needs, companies can minimise downtime and prolong the lifespan of their assets, resulting in significant cost savings.
- Increased Safety and Environmental Compliance: Digital twins can detect potential hazards and monitor emissions, assisting companies in implementing proactive safety measures and ensuring regulatory compliance.
To successfully implement digital twins in oil and gas exploration, companies must:
- Invest in Data Infrastructure: Reliable data collection, storage, and processing infrastructure is essential to support digital twin development and usage. Companies should invest in advanced sensors, IoT devices, and data management systems to facilitate seamless data integration and processing.
- Cultivate a Data-driven Culture: Encourage collaboration between multidisciplinary teams, including geoscientists, engineers, and data analysts, to promote a data-driven approach to exploration and create synergies between domain expertise and digital technologies.
- Embrace Continuous Improvement and Innovation: Digital twins should be continuously refined and updated to reflect changing operational and market conditions. Companies must stay abreast of emerging technological advancements to ensure their digital twins remain at the cutting edge.
Digital twins hold immense potential to revolutionise oil and gas exploration by enhancing accuracy, efficiency, safety, and environmental compliance. By implementing digital twins and embracing a data-driven approach, companies can optimise exploration processes, reduce costs, and improve overall performance.
Addressing Environmental and Safety Concerns with Artificial Intelligence and Connectivity Management
The integration of artificial intelligence and advanced connectivity solutions in the oil and gas industry holds immense potential to minimise the environmental impact of exploration activities while simultaneously enhancing safety for personnel and equipment. These cutting-edge technologies have the transformative power to reshape industry practices, improve operational efficiency, reduce risks, and promote environmental responsibility.
- Environmental Footprint Reduction: AI-based solutions can optimise exploration processes, reduce drilling times, and decrease the number of required wells, ultimately mitigating the ecological impact. By leveraging artificial intelligence algorithms to accurately identify potential reservoirs, companies can carry out focused exploration, effectively reducing land disturbances and minimising ecosystem disruptions.
- Efficient Resource Management: AI-driven real-time data analysis aids in optimising drilling processes, resulting in reduced water, energy, and material consumption. IoT devices and robust connectivity systems can monitor equipment performance and resource usage, facilitating informed decisions to minimise waste and promote sustainable practices.
- Emission Control and Monitoring: Advanced AI-powered analytics can effectively identify and quantify greenhouse gas (GHG) emissions and detect leaks from oil and gas facilities. Simultaneously, IoT devices and connectivity solutions ensure seamless reporting of emission data, enabling proactive measures in managing carbon footprints and ensuring regulatory compliance.
- Real-time Monitoring for Enhanced Safety: AI-enhanced monitoring systems analyse real-time data from sensors and IoT devices installed in exploration sites. These systems enable early detection of potential hazards, such as gas leaks, equipment malfunctions, or geotechnical risks, helping to prevent accidents and safeguard personnel and equipment.
- Predictive Maintenance and Asset Integrity: Integrating artificial intelligence and connectivity solutions in predictive maintenance facilitates early detection of potential equipment failures, reducing the risk of accidents, and minimising downtime. These technologies ensure asset integrity while preventing environmental disasters, such as oil spills, on both offshore and onshore sites.
- Enhanced Emergency Response: In case of accidents or emergencies, AI-powered applications and reliable connectivity can support effective emergency response by rapidly transmitting critical information and coordinating rescue efforts.
- Training and Decision Support: The integration of artificial intelligence and connectivity solutions helps improve personnel training by simulating complex exploration scenarios. Virtual reality (VR) and augmented reality (AR) applications can contribute to training efficiency while minimising risk exposure, leading to better preparedness and increased safety.
The convergence of artificial intelligence and advanced connectivity solutions holds a significant role in minimising the environmental impact of oil and gas exploration while enhancing safety. By embracing these technologies, the industry can achieve more sustainable practices, reduce risks, and maintain compliance with regulatory standards.
byanat as a Catalyst for Sustainable Exploration
Connectivity management plays a crucial role in ensuring the safety of oil and gas exploration operations. byanat's connectivity solutions provide seamless and secure data transmission from exploration sites to central control centres.
This real-time data flow enables continuous monitoring of equipment performance, environmental conditions, and potential hazards. AI-powered analytics can then identify and alert operators of potential risks, allowing for proactive mitigation measures and preventing accidents.
byanat's AI-powered platform enables oil and gas companies to make informed decisions at every stage of the exploration process. By analysing vast amounts of real-time data from sensors, IoT devices, and geological records, byanat's artificial intelligence algorithms can identify potential reservoirs, optimise drilling parameters, and predict subsurface conditions.
This data-driven approach leads to more efficient exploration, reducing drilling times, minimising non-productive time, and increasing the success rate of exploration efforts.
The oil and gas business is being transformed by the combination of artificial intelligence, data analytics, and sophisticated networking solutions. These cutting-edge technologies uncover various advantages by revolutionising exploratory processes, improving drilling operations, and resolving environmental and safety problems. Companies that embrace these advances will not only increase operational efficiency and lower costs, but will also contribute to more sustainable practices and safer workplaces